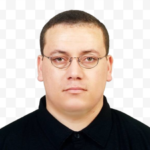
Dr Moussa Hamadache, Research Fellow in Mechatronic Systems for Railways at BCRRE talks about the success of a recent Railway Pantographs project.
Railway pantographs, which are nowadays (with overhead wires) the dominant form of current collection for modern electric trains, have to be inspected on a period basis to make sure that they are operating correctly. This is a time-consuming activity that requires trains to be electrically isolated before staff then access the roof to conduct a manual test on every train in the fleet on a periodic basis.
What does it do?
Funded by RSSB, a team from BCRRE at the University of Birmingham have just completed testing of their DyanPan Demonstrator. This Demonstrator automates pantograph inspections, with results processed in near real-time and compared both to acceptable force and hysteresis limits and previous tests to support trending and deterioration analysis. It consists of an instrumented length of rigid overhead conductor that is set at a relatively steep angle to ‘exercise’ the pantograph down and up. The rigid conductor is supported by gantries equipped with load cells which continually measure the uplift force as a train (or trolley + pantograph in the case of the demonstrator) passes underneath. From this, the contact force generated by the pantograph’s head can be established, and combined with the train’s location (also derived from the load cell measurements) this produces a hysteresis plot of contact force vs pantograph height.
Who was in involved in this project?
Shown below are the core team of Stephen Kent, Dr Moussa Hamadache and Adnan Zentani who installed the DynaPan Demonstrator at QRTC Long Marston in January of this year. The team were supported by Furrer+Frey who supplied the rigid conductor and Computer Controlled Solutions who supplied the instrumentation.
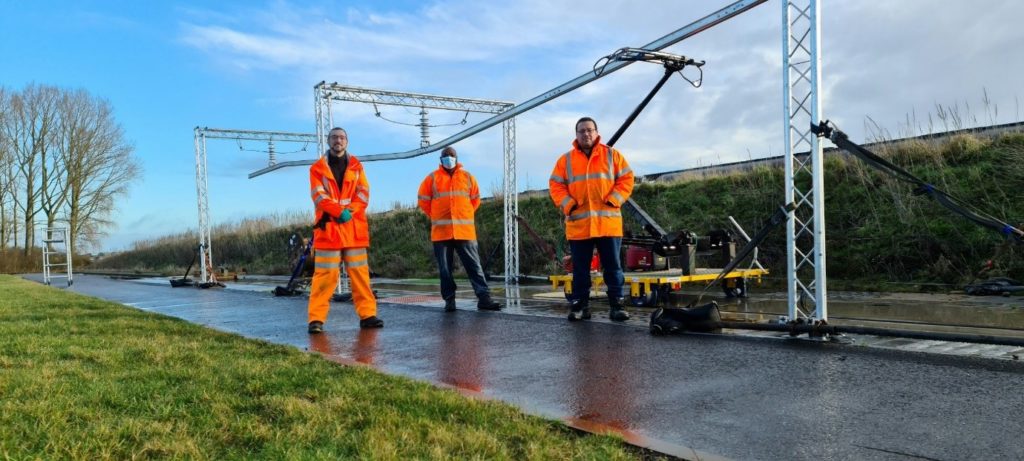
What are the benefits?
The demonstrator proved that the concept works, showing that DynaPan has the potential to considerably reduce the manpower required for pantographs inspection, increase fleet and depot facility availability, while reducing the risk to staff associated with working at height.
The concept was presented earlier this month to the PANTHER SIC (Pantograph Harmonisation for Electrification and Rolling Stock Systems Interface Committee), a cross-industrial group that focusses on developing solutions to Pantograph/Overhead Contact System compatibility challenges. The concept was well-received, with supportive feedback and helpful comments from its members.
What’s next?
We are keen to take this one-step further and test with an actual train and more gantries. This will require further funding and we are exploring options on how we can develop this research work further.