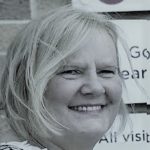
By Rachel Eade MBE, FRSA, Supply Chain Lead at the Birmingham Centre of Rail Research and Education.
Resilience has become a much used word in many contexts in the current pandemic be it, personal resilience, business resilience, NHS resilience or supply chain resilience.
But what is a resilient business?
“One that is able to survive, thrive and create opportunities through time of crisis and change.”
A manufacturing supply chain is complex, diverse and consists of many players; typically with a key customer; a larger company buys in a range of supporting services through its supply chain. These can include a wide range of suppliers from: design, research, prototyping, engineering, manufacturing, logistics, skills, IT, marketing, packaging, finance, quality, HR, work wear, catering, and stationary supplies.
Each of these selected suppliers will then have its own cascade of suppliers to support their company and the specific needs of key customers. As we go down the supply chain and get further away from the key customer the relationship and communication becomes more distant and businesses become more diverse supplying to a wider range of customers and sectors. The beauty of Supply chains is that they are flexible having to be responsive to change, varying demands and innovation.
So resilience is an important feature for every company its supply chain. Every business plays an interconnecting part in the supply chain process and all behaviours have a knock on effect up and down and across the whole supply chain. In this Covid period, we all need to be as resilient as we can for both today, tomorrow and the future.
Developing resilience can be both complex and personal. It involves a combination of inner strengths and outer resources, and there isn’t a universal formula for becoming more resilient. All people and all businesses are different: while one person might develop symptoms of depression or anxiety following a traumatic event, another person might not report any symptoms at all; one business may cease to trade as a result of the loss of a key customer, another may diversify and continue to grow.
A combination of factors contributes to building resilience, and sadly there isn’t a simple to-do list to work through adversity. In one longitudinal study, a number of protective factors were identified as inherent in resilient businesses, these included whole business cohesion, and that people are a business’s key asset particularly identifying strong leadership, good interpersonal relationships, along with sound financial understanding and footing. Across the supply chain we need to seek suppliers and customers who demonstrate characteristics of resilience that include: good communications, good forecasting, and clear processes especially regarding change, ability (and desire) to negotiate and listen. In supply chain management some key features of supplier selection and development help identify features of resilience. Reaching out to and using external resources and expertise is also characteristic of a resilient and strong business.
Some of the areas presenting resilience challenges for businesses today include:
The ability to adapt business models in light of business interruption especially in periods of crisis, having a leadership team that can recognise early signs of change and distress, has good communication with both customers and suppliers is critical in being able to respond to business crisis’s and develop and implement a response and recovery plan. As the announcement of England’s second lockdown period has shown us, recovery plans need to be flexible and able to respond to external factors that are out of our control.
The current pandemic and Government encouragement to work from home has accelerated digitisation in many areas. For manufacturing suppliers this is reflected in the adoption of industry 4.0 across manufacturing processes and in the ability to trade, communicate and market on online. Cyber-crime and security is critical in all manufacturing digitisation. For many smaller businesses this is a new asset and requires investment, not only financial but in skills and training across the workforce.
A recent digital skills needs analysis has identified that 95% of the manufacturing workforce require IT upskilling. For many years we have known the manufacturing sector has an aging workforce and therefore, its skills (both new and traditional skill training) is essential. Resilient companies have a training budget, training plans for all employees – at all levels, have apprentices, engage with local schools and colleges and celebrate success and achievement.
Keeping abreast of sector demands and changes is critical to long term business growth. Innovation in products and processes is constant, the key drivers of digitalisation and decarbonisation across a number of sectors but currently are critical in the transport sector notably in the electrification of not only cars but buses and trains. All businesses in a supply chain have a need to listen out for innovation trends and how these may impact on their product, processes and services. Change really is inevitable!
New legislation and changing regulations, are often driven by innovation and global demands particularly with regard to the environment. The UK`s exit from the European Union highlights every businesses need to understand the upcoming changes and address areas of relevance. There will be something for every business to action and prepare for from January 2021. Good EU exit preparedness is an excellent sign of a resilient company.
There is information and support freely available for all the areas identified, please do reach out to your Trade membership organisation, Chamber of Commerce, Growth Hub’s, and Universities, along with your bank, accountant or legal advisors.
Now is the time to reach out and seek support, all these organisations have fully adopted the full range of work from home technologies across their teams to help every company become one that is able to survive, thrive and create opportunities through this time of crisis and change.
At the Birmingham Centre for Railway Research and Education we offer expert research advice and practical support via our education programmes and staff.
We also have our Digi-Rail project that offers free support to SMEs focusing on digitalisation not only for supply chain and businesses within the railway industry but broadly within the transport sector and beyond. Learn more about the offering at: www.birmingham.ac.uk/Digi-Rail.
We are also home to the UK’s largest dedicated business-to-business networking organisation for connecting the rail industry and its supply chain, across the UK, Europe and world-wide. The Rail Alliance is the It is a membership organisation that sits at the very heart of the rail supply chain and has evolved as a leading representative of the UK rail supply chain community. The Rail Alliance exists for its member organisations, working across the industry to drive growth; bringing customers, suppliers and supply chain opportunities together; enabling and support innovation; and, ultimately, supporting the entire rail supply chain to thrive. To find out more visit: www.railalliance.co.uk/