In this case study, we hear from Benjamin Jenkins (EngD Formulation Eng FT), who has been making use of BlueBEAR to enable his research into powder simulation and issues surrounding calibration.
You probably don’t think about how we use powders in manufacturing on a day-to-day basis and I wouldn’t blame you! They are however, the second most manipulated material in industry, yet our understanding of them remains in the stone age. Powder simulation has become an extremely promising technology to allow us to model powders, but a major problem is calibration. In this article, I hope to give you a lightspeed introduction to our research and showcase how BlueBEAR is essential in unlocking the potential of powder simulation!
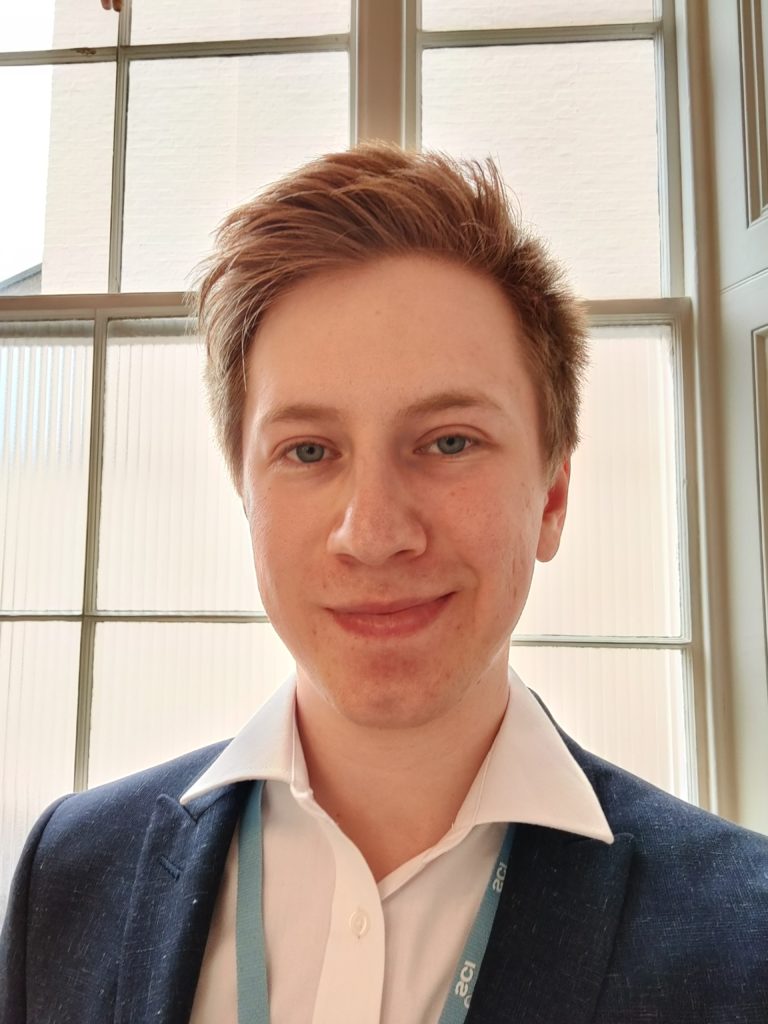
In almost any manufacturing process there will be powder involved at some point. Even the device that you are reading this on has components that were made from extremely pure silica sand. Yet despite this, powders are very poorly understood due to how complex their behaviour is. Due to this complexity, the way we design powder handling equipment has remained simple and heavily reliant on empirical correlations that are wrong half of the time.
BlueBEAR allows us to run hundreds of these simulations at a time
Fluid processing has been a continuous process for centuries (think of oil refineries). Yet most powder processing remains batch based to this day and currently one of the biggest areas of powder technology research is making pharmaceutical process continuous. I think the image by the New York Times below sums up the difficulty of powders very well. Although maybe this just helps me feel better about myself when I tell others that powders are the hardest area of physics!
So, what can we do? Well, a promising option is powder simulation. Many methods for simulating powders exist from modelling a powder as an average cloud of particles to modelling each particle as its own individual element and throwing a bunch together. In any case, the simulation is a simplified version of reality as we simply don’t know the actual physics that goes on. In our research, we use the discrete element method (DEM) approach where each particle is modelled as its own free element that can move around under gravity. We even model the energy dissipation due to frictional forces between particles as well as the cohesion forces that hold particles together. (Cohesion is the reason you need a sieve to get those pesky lumps out of flour when baking a cake!)
With powder simulation we can make a computer model of our manufacturing equipment and run some powder through it. This could be at the design stage to test how well our design works or, for example, to work out what is causing powder to jam once the equipment is already built. Great right? Well, we aren’t quite there yet. For the simulation to give us correct results we need to tell it what the properties of our particles are. How frictional are they? How bouncy are they? A slight change in the friction of the particles can greatly change the behaviour of the bulk powder!
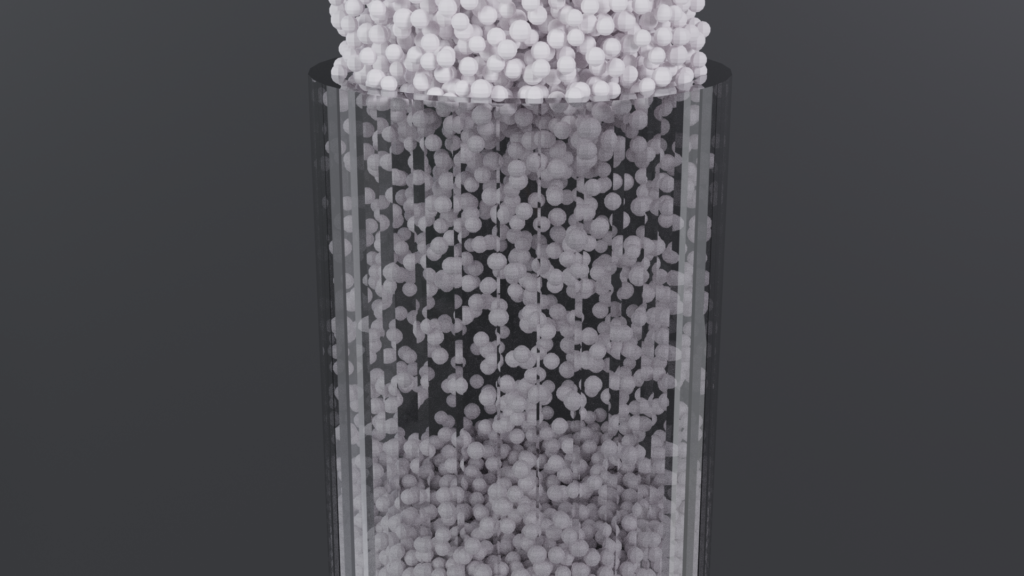
But how do we find the properties of the particles I hear you ask? Well, that’s what we are trying to do! The ideal case would be to just measure them directly, but this is extremely difficult to do. Instead, we want to take some easy measurement of a powder, which could be as simple as pouring a powder into a pile on a flat surface and measuring the angle of that pile with the flat surface and inferring the microscopic particle properties from that measurement.
This is where BlueBEAR comes in. By running tens of thousands of simulations, forming a pile of powder and each time slightly changing the microscopic properties of the particles in the pile, we can build up a dataset that links the angle of that pile to the microscopic properties. Of course, in reality, it is not as simple as just making a pile of powder and measuring the angle, but I digress. BlueBEAR allows us to run hundreds of these simulations at a time or if we want to run one big simulation with even more particles then we can use all those cores on one job! Running so many simulations also produces many terabytes of data, which is not a lot for big research projects but from one PhD is significant. Having the research data store means we don’t have to worry about the amount of data we are generating.
BlueBEAR is essential in unlocking the potential of powder simulation!
I could talk about powders all day but to spare you from that torment I will conclude! BlueBEAR is flexible and powerful, CPU compute and data store that allows us to create a novel powder simulation calibration methodology that will make such simulations accessible to everyone and increase their adoption in industry, allowing us to design better powder handling and processing equipment.
We were so pleased to hear of how Benjamin is able to make use of what is on offer from Advanced Research Computing, particularly to hear of how he has made use of BlueBEAR HPC– if you have any examples of how it has helped your research then do get in contact with us at bearinfo@contacts.bham.ac.uk. We are always looking for good examples of use of High Performance Computing to nominate for HPC Wire Awards – see our recent winners for more details.