In this case study, we hear from Vincenzo Brachetta (School of Metallurgy and Materials), who has been working on prediction of residual stresses in materials science using the high-performance cluster BlueBEAR and the Research Data Storage, both housed at the University of Birmingham. He is also a member of the Birmingham Environment for Academic Research (BEAR) Champions group.
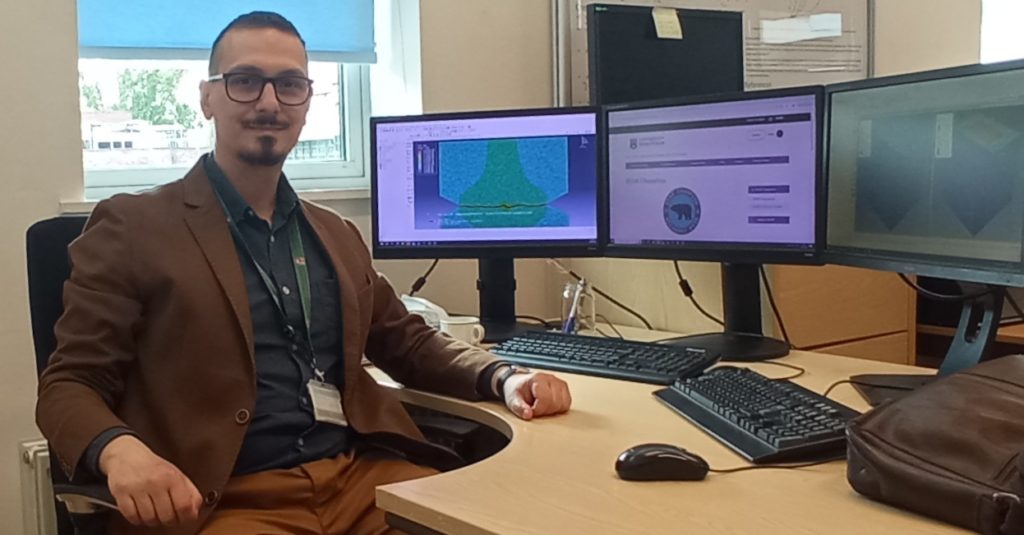
I am a researcher and computational scientist specialised in the study of complex physical-mathematical problems through numerical approximation. I hold a Master of Science in Construction Engineering with First-Class Honours and have completed a set of studies for a PhD at the School of Metallurgy and Materials, College of Engineering and Physical Sciences, University of Birmingham.
Access to a supercomputer like BlueBEAR enables the use of parallel computing capabilities, allowing multiple simulations to run concurrently
My recent research, among other interests, has concentrated on the finite element modelling of the additive manufacturing process, specifically aimed at predicting residual stresses and fatigue behaviour of a titanium alloy. The long-term goal of my studies is to minimise the material and energy waste associated with the production and repair of mechanical components, such as the turbine blades used in aerospace.
Problem setting
One of the unavoidable consequences of component production, and particularly in additive manufacturing, is the generation of process-induced residual stresses. These are internal plastic stresses that persist after the production process has concluded. They are generated as a result of high temperature gradients that lead to localised material expansion and, consequently, plastic deformations. The adverse effects of residual stresses include a reduction in fatigue life during in-service conditions.
Furthermore, rapid cooling during welding and additive manufacturing of titanium alloys often results in a transformation of part of the material into ‘martensite’, a brittle phase that further reduces the component’s lifespan during in-service cyclic loading.
It is not merely the power of BlueBEAR that is crucial in advancing this field of study, but also the comprehensive IT infrastructure at the University of Birmingham
In summary, residual stresses and the martensitic phase are generated during the interaction between the laser heat source and the material. Thanks to the finite element method, the predicting capabilities for this study can rely on high-fidelity numerical simulations, like those developed in SIMULIA/Abaqus, integrated with FORTRAN and Python. For example, Figure 1 shows the visualisation of a numerical study on phase transformation.
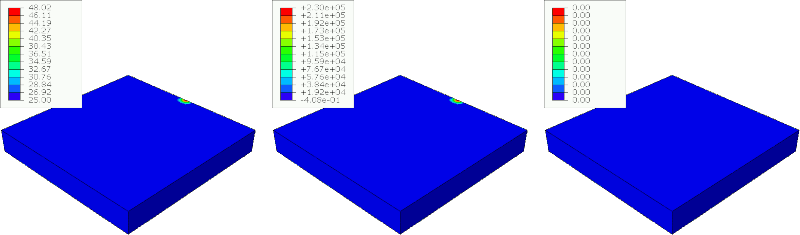
Computational framework and BlueBEAR
Unlike a single laser scan, which models laser welding, additive manufacturing operates through a rapid sequence of multiple laser scans that melt the material to create the final component. In a laboratory, a technical operator can manipulate a variety of parameters, typically referred to as the ‘process window’ in materials science. Consequently, one of the current challenges lies in predicting the residual stresses across the entire process window of the material. If undertaken experimentally, this requires the manufacture and testing of a large number of samples, making the procedure laborious. Additionally, assessing residual stresses in different materials necessitates the production and analysis of a new series of samples.
This infrastructure (BEAR) has continuously improved over the years and is maintained at the highest level, including a reliable, fast, and secure Research Data Store, along with advanced software management systems.
By employing a ‘process model’, it is possible to accurately predict residual stresses at the end of the cooling phase. The model developed and studied is based on the non-linear transient heat equation coupled with material thermo-viscoplasticity. To solve this computational problem, the domain of interest and the governing equation are approximated through the finite element method. However, even though numerical simulations can significantly reduce experimental work, this task can be computationally intensive to perform on a standard desktop machine.
Two visualisations of multiple laser scans simulations are depicted in Figure 2 and Figure 3, where different hatch spacing values have been used (respectively 40, 80, and 100 µm).
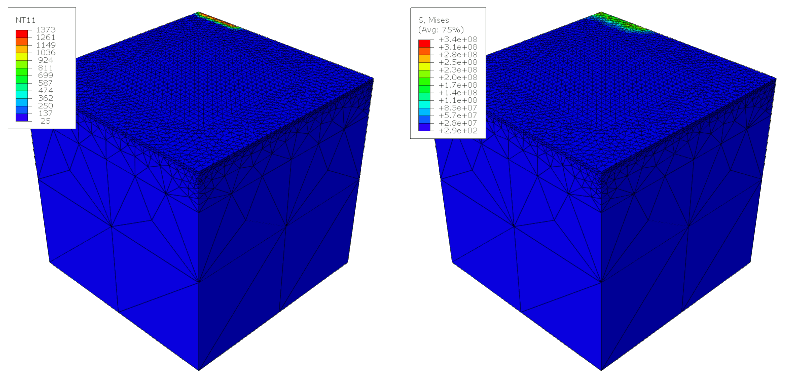
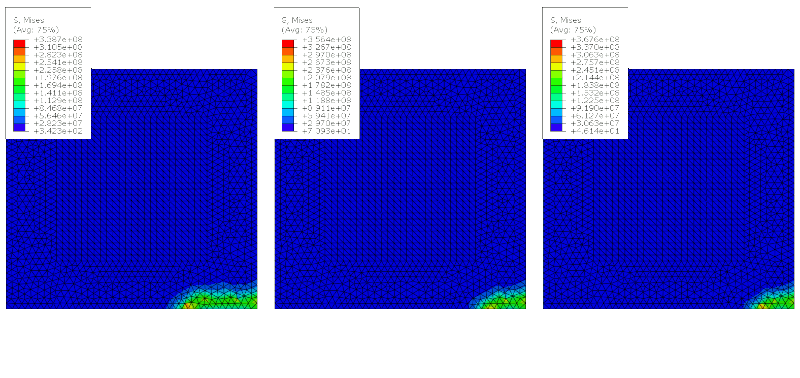
Access to a supercomputer like BlueBEAR enables the use of parallel computing capabilities, allowing multiple simulations to run concurrently, with each simulation leveraging multiple cores simultaneously. It is not merely the power of BlueBEAR that is crucial in advancing this field of study, but also the comprehensive IT infrastructure at the University of Birmingham. This infrastructure has continuously improved over the years and is maintained at the highest level, including a reliable, fast, and secure Research Data Store, along with advanced software management systems.
The capabilities of BlueBEAR prove invaluable across disciplines where an ordinary machine cannot complete numerical tasks within a reasonable time frame, thus surpassing the limitations of standard computational equipment.
Technical details
Access to BlueBEAR is facilitated through Putty, an open-source terminal emulator, which provides secure access to the supercomputer’s GNU/Linux interface. From the GNU/Linux Bash terminal, simulation jobs can be submitted and monitored using Slurm Workload Manager, a free and open-source job scheduler. This scheduler enables the launching of simulations via SIMULIA/Abaqus, which can be integrated with user subroutines written in FORTRAN. Finally, the results can be accessed through a custom Python script designed to read the numerical values in the solution database saved by the finite element computer program.
Conclusion
BlueBEAR has proven to be essential to complete the research and so successfully contribute to this research field. More generally, the high-performance cluster is fundamental for studies where researchers need to explore numerical models and gain a deeper understanding of model behaviour. The capabilities of BlueBEAR prove invaluable across disciplines where an ordinary machine cannot complete numerical tasks within a reasonable time frame, thus surpassing the limitations of standard computational equipment.
We were so pleased to hear of how Vincenzo was able to make use of what is on offer from Advanced Research Computing, particularly to hear of how he has made use of BlueBEAR HPC and its many cores – if you have any examples of how it has helped your research then do get in contact with us at bearinfo@contacts.bham.ac.uk. We are always looking for good examples of use of High Performance Computing to nominate for HPC Wire Awards – see our recent winners for more details.