To celebrate Responsible Business Week we will be posting a series of blogs on this topic. In this post, Lecturer in Management Dr. Vivek Soundararajan offers his own perspective on sustainable global supply chains.
Midday in South India, the weather is terribly hot (somewhere between 36 and 38 degree Celsius) and the long-drives, undisciplined eating, lack of water intake, too much talking and observations have combined to making me feel exhausted. Due to this, I initially ignored receiving an email inviting me to write a blog for the upcoming “Responsible Business Week”. However, when I had time and energy to reflect, I thought this is a great way to let the world know the realities of sustainable global supply chains from the field of what I have observed and how this impacts on daily lives.
Since 2011, I have been studying the largest knitwear garment-exporting cluster in India. This had led to interesting discoveries and I would like to share with you some of my observations:
Marginalized workers
The academic, policy and practice circles of sustainable global supply chains are too isolated from the marginalized i.e. workers. I have spent months travelling around the most rural parts of South India to listen to the stories of workers, would-be workers and their families. Everyone is different, some are poor, some extremely poor, most of them are uneducated. Sadly, most also do not have any idea about how the industry works or their own rights as workers. Fifty page policy documents or professional training does not make any sense to them. They enter the industry with a lot of hope and they do whatever they can to create a better life for themselves and their family. One thing became clear; their voices are not heard or improperly understood – even by local NGOs. Actors, including brands and local governments, are also too far away from the world of workers, there is a need for real engagement with the marginalized.
Positive developments
There are many positive developments needful of acknowledgment, for example, I visited a garment factory that is 100% powered by solar energy. The factory employs nearly 1500 workers and makes an annual turnover of Indian National Rupees (INR) 100 Crores supplying to brands like Ralph Lauren and Fila. The industry has spent so much on the local community and infrastructure development and is on its ways towards attaining Zero Liquid Discharge (ZLD).
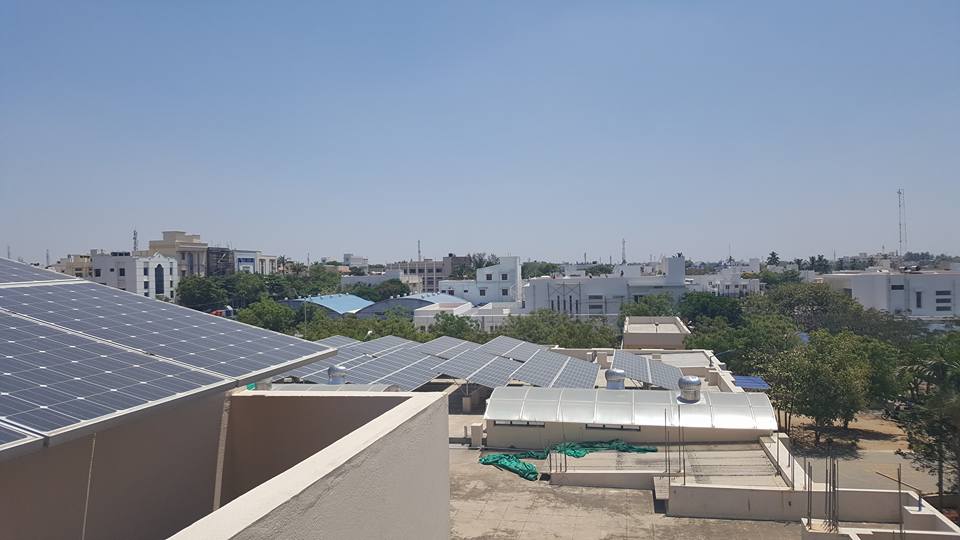
In addition, some factories are empowering underprivileged women workers through education, training and scholarships. While it is our responsibility to highlight the problems, it is also our responsibility to acknowledge these positive developments.
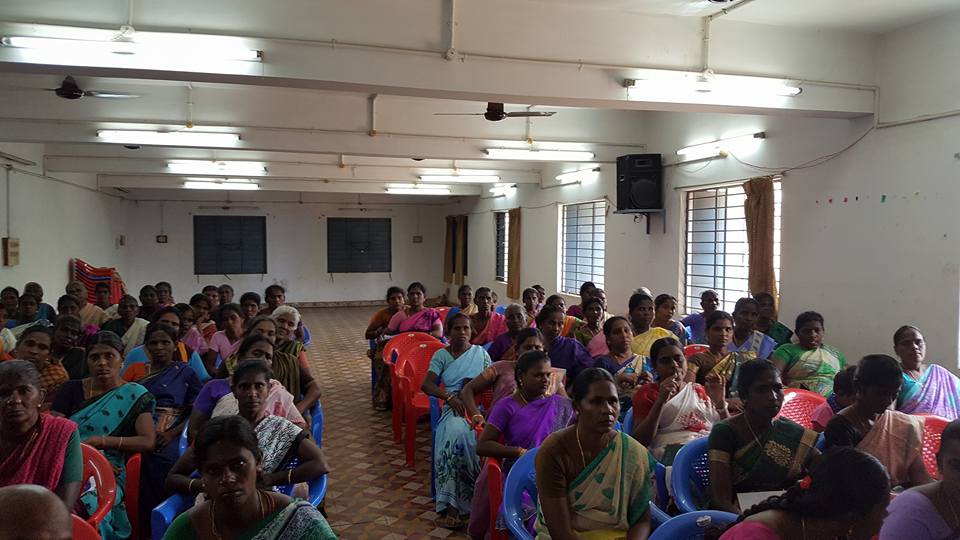
Voluntary governance/Certification
Voluntary governance mechanisms (i.e. sustainability standards or certifications) that are used to govern sustainability in global supply chains are not voluntary, they are forced upon suppliers. While large suppliers can easily adopt them (although with some hesitance), unfortunately small ones are not able to, as they are resource-deprived. Nevertheless, for survival, small ones will still adopt them, but, some engage in various evasion practices to maintain them
Many small suppliers are not purposefully engaging in evasion as they cannot afford to buy and maintain certifications, they are not given a price increase nor they are given incentives to buy or maintain them. Such insensitive mechanisms increase their indebtedness to banks. This highlights how the local policies and politics too are not in favor of them.
Furthermore, certifications are not doing what they are supposed to do; they are distracting everyone from real issues. The conversation, in academic, practice and policy circles is gradually shifting from how to genuinely improve sustainability to how to make suppliers comply with certifications. The outcome is emergence of a new certification everyday and that certification organizations are growing bigger while the issues still remain unaddressed. Certifications are too generic; they focus a lot on ticking boxes; the auditors are not properly trained and some are corrupted; there is no proper dialogue mechanism; marginal stakeholders are not taken into consideration; there is too much competition among certification organizations; and they shift the responsibility away from the brands and this is dangerous.
Management style
Even in factories that make an annual turnover of more than INR 100,00,00,000, the management style is ad-hoc and informal. Divisions are just for the sake of paperwork. Owners have complete control of everyday happenings, and will interfere into the smallest of issues. Does this mean they are control freaks or that the management style is inferior? No, this is just how they work. They do not have much exposure to the corporate world and they are extremely proud of their achievements, business is their baby that they like to have eyes on every thing inside their factory. With the second generation gradually taking over, things will change. However, we should understand that there are different ways of organizing.
Human Resource Management
There is a great need for developing human resource management capabilities of suppliers. Even large factories lack this capability. Labor shortage is a serious issue and they do not seem to predict the need for human resources and plan accordingly. Furthermore, they do not engage in activities to retain their workers. Human Resource Managers, even with MBAs, are not engaging with workers to understand their needs and demands; instead they act as mere record keepers and signing authorities. This has to change. For the industry to move forward in terms of sustainability, the human resource management capabilities of the suppliers must be developed.
Dr. Vivek Soundararajan is a Lecturer in Management in the Department of Strategy and International Business at Birmingham Business School. He can be reached at v.soundararajan@bham.ac.uk.
More about Responsible Business Week
Get engaged with the brighter side of business by downloading the guide to Responsible Business Week and following the conversation on Twitter via #RBweek.